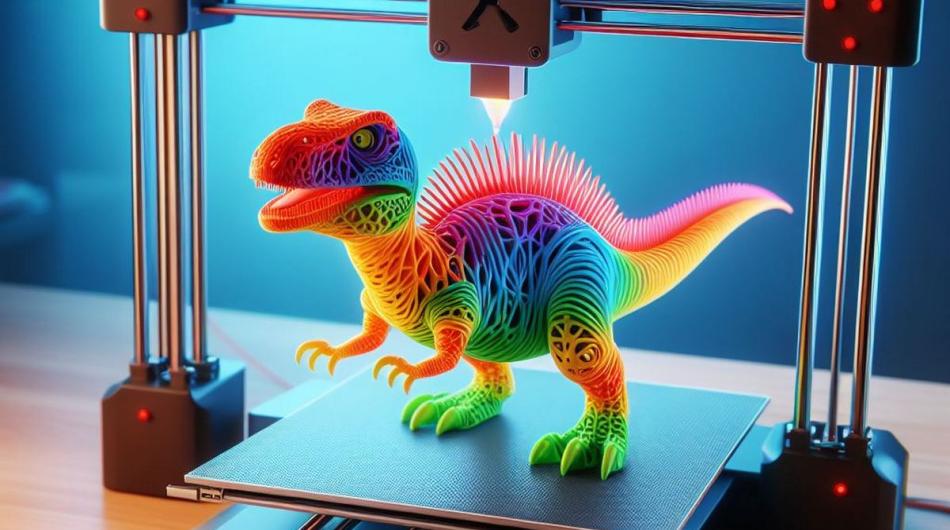
4D printing is an emerging technology that combines the principles of 3D printing with the concept of smart materials, resulting in printed objects that can change their shape or properties over time in response to external stimuli. This innovative approach to additive manufacturing has the potential to revolutionize various industries, from biomedical engineering to aerospace and beyond. In this comprehensive article, we will explore the fundamentals of 4D printing, its applications, challenges, and future prospects.
The Concept of 4D Printing
Definition and Overview
4D printing is an extension of 3D printing technology, where the printed objects are designed to transform their shape, functionality, or properties over time when exposed to specific stimuli, such as heat, light, moisture, or electric current. The "4D" in 4D printing refers to the fourth dimension, which is time, as the printed objects are not static but can change and adapt to their environment.
The concept of 4D printing was first introduced by Skylar Tibbits, a researcher at MIT's Self-Assembly Lab, in collaboration with Stratasys, a 3D printing company, in 2013. Tibbits demonstrated the potential of 4D printing by creating a simple strand that could self-fold into a cube when exposed to water, showcasing the ability of printed objects to transform and adapt post-production.
Key Elements of 4D Printing
4D printing involves three key elements: 3D printing technology, smart materials, and computational design.
- 3D Printing Technology: 4D printing relies on the same additive manufacturing processes used in 3D printing, such as fused deposition modeling (FDM), stereolithography (SLA), and selective laser sintering (SLS). These technologies enable the creation of complex geometries and structures that can be programmed to change shape or properties over time.
- Smart Materials: The materials used in 4D printing are designed to respond to specific stimuli, such as temperature, humidity, light, or magnetic fields. These materials can be programmable matter, such as shape memory polymers, hydrogels, or multi-material composites, which can change their shape, color, or other properties when exposed to the appropriate stimulus.
- Computational Design: To create 4D printed objects, designers use computational tools and algorithms to simulate and predict the behavior of the smart materials under different conditions. This involves modeling the material properties, the desired shape transformations, and the external stimuli that trigger these changes. The resulting digital models are then translated into instructions for the 3D printer to fabricate the object.
Advantages of 4D Printing
4D printing offers several advantages over traditional manufacturing methods and 3D printing:
- Adaptability: 4D printed objects can adapt to their environment and change their shape or properties in response to external stimuli, making them suitable for applications where flexibility and responsiveness are required.
- Functionality: By incorporating smart materials and designed shape transformations, 4D printed objects can perform specific functions or tasks, such as self-assembly, self-repair, or self-adjustment, without the need for additional components or manual intervention.
- Material Efficiency: 4D printing can reduce material waste and improve resource efficiency by creating objects that can change their shape or properties post-production, eliminating the need for multiple parts or assemblies.
- Customization: Like 3D printing, 4D printing enables the creation of highly customized and personalized objects that can be tailored to specific applications or user needs.
Applications of 4D Printing
4D printing has the potential to impact various industries and sectors, from healthcare and biomedical engineering to aerospace, automotive, and construction. Some of the most promising applications of 4D printing include:
Biomedical Engineering
In the biomedical field, 4D printing can be used to create dynamic and adaptive medical devices, implants, and tissue engineering scaffolds. Some examples include:
- Self-fitting Stents: 4D printed stents that can adjust their shape and size in response to changes in the patient's blood vessels, providing better fit and reducing the risk of complications.
- Shape-shifting Implants: Implantable devices that can change their shape or properties over time to adapt to the patient's anatomy or healing process, such as self-adjusting orthopedic implants or self-expanding vascular grafts.
- Smart Wound Dressings: 4D printed wound dressings that can sense and respond to changes in the wound environment, such as pH or moisture levels, and release drugs or other agents to promote healing.
- Tissue Engineering Scaffolds: 4D printed scaffolds that can guide and stimulate tissue growth and regeneration, by changing their shape or properties in response to cellular cues or external stimuli.
Aerospace and Automotive
In the aerospace and automotive industries, 4D printing can be used to create lightweight, adaptive, and multifunctional structures that can improve performance, efficiency, and safety. Some examples include:
- Morphing Wings: 4D printed aircraft wings that can change their shape in response to different flight conditions, such as turbulence or high-speed maneuvers, to optimize aerodynamic performance and fuel efficiency.
- Self-deploying Structures: Compact, lightweight structures that can self-assemble or self-deploy in response to specific triggers, such as temperature or pressure changes, for applications such as satellite antennas or emergency shelters.
- Adaptive Suspension Systems: 4D printed automotive suspension components that can adjust their stiffness or damping properties in real-time, based on road conditions or driver preferences, to improve ride comfort and handling.
- Self-repairing Components: 4D printed parts that can sense and respond to damage or wear, by self-healing or self-reinforcing their structure, to extend their lifespan and reduce maintenance requirements.
Construction and Architecture
4D printing can also revolutionize the construction and architecture sectors, by enabling the creation of smart, adaptive, and sustainable built environments. Some examples include:
- Self-assembling Structures: 4D printed building components that can self-assemble on-site, reducing construction time and labor costs, and enabling the creation of complex, customized structures.
- Adaptive Facades: 4D printed building envelopes that can change their shape, color, or transparency in response to environmental conditions, such as sunlight or temperature, to optimize energy efficiency and occupant comfort.
- Self-healing Infrastructure: 4D printed concrete or asphalt that can self-repair cracks or damage, by incorporating self-healing agents or shape memory materials, to extend the lifespan of roads, bridges, and buildings.
- Smart Ventilation Systems: 4D printed ventilation ducts or grilles that can adjust their shape or porosity in response to changes in air quality or occupancy, to improve indoor environmental quality and energy efficiency.
Other Applications
4D printing has potential applications in many other fields, such as:
- Fashion and Textiles: 4D printed garments or accessories that can change their shape, color, or texture in response to body heat, moisture, or other stimuli, for functional or aesthetic purposes.
- Robotics and Soft Robotics: 4D printed actuators, sensors, or soft robots that can change their shape or properties in response to electrical or mechanical stimuli, for applications such as grippers, locomotion, or haptic interfaces.
- Education and Entertainment: 4D printed toys, puzzles, or educational models that can demonstrate scientific concepts or engage users through interactive shape transformations.
Materials and Technologies for 4D Printing
The success of 4D printing relies heavily on the development of smart materials and advanced printing technologies that can enable programmable shape transformations and responsive behavior.
Smart Materials
Smart materials are the key enablers of 4D printing, as they can respond to external stimuli by changing their shape, color, or other properties. Some of the most common types of smart materials used in 4D printing include:
- Shape Memory Polymers (SMPs): Polymers that can be programmed to "remember" a specific shape and return to it when exposed to a particular stimulus, such as heat or light. SMPs are widely used in 4D printing due to their versatility, biocompatibility, and ease of processing.
- Shape Memory Alloys (SMAs): Metallic alloys, such as Nitinol (nickel-titanium), that can undergo reversible shape changes when heated or cooled. SMAs are known for their high strength, durability, and large recoverable strains, making them suitable for applications that require significant shape transformations.
- Hydrogels: Polymer networks that can absorb and retain large amounts of water, and change their shape or volume in response to stimuli such as temperature, pH, or ionic strength. Hydrogels are particularly useful for biomedical applications, as they can mimic the properties of natural tissues and support cell growth.
- Liquid Crystal Elastomers (LCEs): Polymeric materials that combine the properties of liquid crystals and elastomers, enabling reversible shape changes in response to heat, light, or electric fields. LCEs can exhibit large, programmable shape transformations and have potential applications in soft robotics and adaptive optics.
- Multi-material Composites: Combinations of different materials, such as polymers, metals, or ceramics, that can be printed together to create objects with heterogeneous properties and programmable shape transformations. Multi-material composites offer greater design flexibility and can enable more complex and multi-functional 4D printed structures.
Printing Technologies
4D printing relies on advanced additive manufacturing technologies that can process smart materials and create complex, programmable structures. Some of the most common printing technologies used in 4D printing include:
- Fused Deposition Modeling (FDM): A widely used 3D printing technique that involves extruding molten thermoplastic filaments layer by layer to create a 3D object. FDM can be adapted for 4D printing by using shape memory polymers or multi-material composites as filaments.
- Stereolithography (SLA): A 3D printing process that uses a laser to selectively cure and harden a liquid photopolymer resin layer by layer. SLA can be used for 4D printing by incorporating smart materials, such as shape memory polymers or hydrogels, into the resin formulation.
- Selective Laser Sintering (SLS): A powder-based 3D printing technique that uses a laser to sinter and fuse together powdered materials, such as polymers, metals, or ceramics, into a solid object. SLS can be used for 4D printing by using shape memory alloys or multi-material composites as the powder feedstock.
- Inkjet Printing: A printing method that involves depositing tiny droplets of liquid material, such as inks or polymers, onto a substrate to create a pattern or structure. Inkjet printing can be used for 4D printing by using smart materials, such as hydrogels or liquid crystal elastomers, as the ink formulation.
- Direct Ink Writing (DIW): A 3D printing technique that involves extruding a viscous ink or paste through a nozzle to create a 3D structure. DIW can be used for 4D printing by using smart materials, such as shape memory polymers or multi-material composites, as the ink formulation.
Challenges and Future Prospects
Despite the significant progress made in 4D printing research and development, several challenges and opportunities remain to be addressed to fully realize the potential of this technology.
Technical Challenges
- Material Development: One of the main challenges in 4D printing is the development of new smart materials that can exhibit desired shape transformations and responsive behavior while maintaining good printability, stability, and durability. This requires a deep understanding of the structure-property relationships of these materials and the ability to fine-tune their composition and processing conditions.
- Printing Process Optimization: 4D printing often involves complex, multi-step printing processes that require precise control over material deposition, curing, and post-processing. Optimizing these processes to achieve high resolution, accuracy, and repeatability is crucial for the successful fabrication of 4D printed objects.
- Modeling and Simulation: Designing 4D printed objects requires sophisticated computational tools that can predict and simulate the behavior of smart materials under different stimuli and loading conditions. Developing accurate and efficient modeling and simulation techniques is essential for the rational design and optimization of 4D printed structures.
- Scalability and Manufacturing: Scaling up 4D printing from small-scale prototypes to large-scale, high-volume manufacturing remains a challenge. This requires the development of robust, reliable, and cost-effective printing technologies and the establishment of standardized processes and quality control measures.
Future Prospects
- Multi-functional 4D Printing: One of the future directions of 4D printing is the development of multi-functional objects that can perform multiple tasks or respond to multiple stimuli simultaneously. This could involve the integration of different smart materials, sensors, and actuators into a single 4D printed structure, enabling more complex and adaptive behavior.
- Bioinspired 4D Printing: Nature provides many examples of adaptive, responsive, and self-organizing structures, such as the Venus flytrap or the chameleon skin. Bioinspired 4D printing seeks to learn from and mimic these natural systems to create more efficient, sustainable, and intelligent man-made structures.
- 4D Printing for Sustainability: 4D printing has the potential to contribute to sustainability by enabling the creation of adaptive, self-repairing, and self-recycling structures that can reduce waste and extend the lifespan of products. This could involve the development of biodegradable or recyclable smart materials and the design of closed-loop, circular economy systems.
- 4D Printing for Space Exploration: 4D printing could play a significant role in space exploration by enabling the creation of lightweight, compact, and self-deploying structures that can adapt to the harsh conditions of space. This could include self-assembling habitats, self-repairing spacecraft, or self-adjusting solar panels that can optimize their orientation and efficiency.
Conclusion
4D printing is a groundbreaking technology that combines the principles of 3D printing with the concept of smart materials, enabling the creation of dynamic, adaptive, and responsive structures that can change their shape or properties over time. With its potential to revolutionize various industries, from biomedical engineering to aerospace and construction, 4D printing offers exciting opportunities for innovation, sustainability, and problem-solving.
However, the development and adoption of 4D printing also face several challenges, such as the need for advanced materials, printing technologies, and computational tools, as well as the scalability and manufacturability of 4D printed objects. Addressing these challenges requires a multidisciplinary approach that brings together experts from materials science, engineering, computer science, and other fields.
As research and development in 4D printing continue to progress, we can expect to see more sophisticated and multi-functional 4D printed structures that can adapt to their environment, perform complex tasks, and contribute to sustainability. From self-assembling medical implants to shape-shifting aircraft wings and self-repairing infrastructure, the possibilities of 4D printing are vast and exciting.
In conclusion, 4D printing represents a new frontier in additive manufacturing and smart materials, with the potential to transform the way we design, fabricate, and interact with objects and structures. As this technology continues to evolve and mature, it will undoubtedly play a significant role in shaping the future of many industries and addressing some of the most pressing challenges facing our world today.